The Future of Manufacturing #2 - The Smart Factory Stack
Since my last post, I’ve attended two industry conferences and had over a dozen conversations with various founders to gain a better understanding of the intricacies and pain points faced by the manufacturing industry. Let me start by saying this is not a straightforward industry by any means. The vast diversity of manufacturers—in terms of industry, size, processes, and digital maturity—means there's no one-size-fits-all solution.
Throughout these discussions, I found myself asking a recurring question: how does this solution fit into, add, or replace existing systems? This post aims to share my findings and latest thinking as we craft our thesis on the Future of Manufacturing.
Traditional Factory Layers
Let’s start by abstracting a basic framework that holds true for most manufacturers today. This framework consists of three key layers integral to any manufacturing facility:
The Enterprise Layer: This top layer consists of executive leadership and decision-makers defining the overall strategy and goals of the facility. It includes functions such as finance, marketing, and supply chain management, ensuring alignment with broader business objectives.
The Management Layer: This layer oversees and coordinates production activities. It involves middle managers and supervisors ensuring production goals are met, resources are allocated effectively, and issues on the production floor are addressed. It bridges the front line and the enterprise vision.
The Front Line Production Layer: This layer includes the machinery, equipment, sensors, and workforce directly involved in producing goods. The focus is on efficiency, quality control, and maintaining optimal production levels.
Depending on the size of the manufacturer, these layers may be more or less distinct.
The Manufacturing Alphabet Soup
With the backdrop of the three key factory layers, we can then examine the “alphabet soup” of traditional manufacturing software and systems and how they integrate into each layer of the traditional factory. This alphabet soup commonly includes:
ERP (Enterprise Resource Planning): Software that helps manage all main business activities, such as finance, supply chain, operations, reporting, manufacturing, and human resources.
MES (Manufacturing Execution System): A system that tracks and controls the production process on the factory floor, helping to ensure that manufacturing operations run smoothly and efficiently.
SCADA (Supervisory Control and Data Acquisition): A system that allows operators to monitor and control equipment and processes from a central location, often remotely.
PLC (Programmable Logic Controller): Special computers used to control machinery and processes in the factory, making sure everything operates correctly and consistently.
APM (Asset Performance Management): Tools that help keep track of how well machines and equipment are working, aiming to improve their performance and prevent breakdowns.
Depending on various factors such as the size, level of sophistication, type of manufacturing process, or industry, a factory may utilize all or none of the above.
The below diagram provides a helpful visualization of the traditional factory layers and systems:
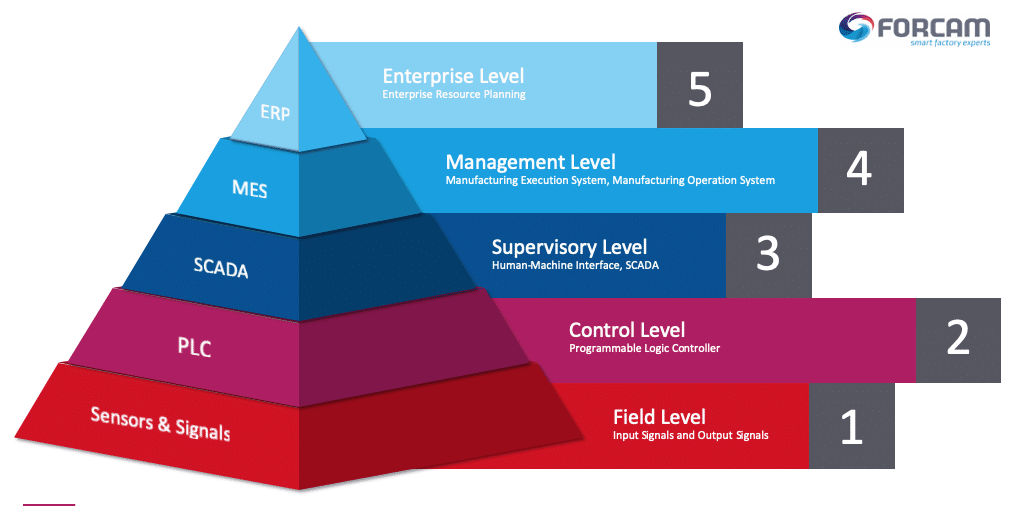
The Industry 4.0 Matrix
The traditional factory stack described above has historically been rigid and siloed, with data collected in isolated platforms that cannot be leveraged across the organization. Based on conversations to date, the new stack for smart factories will be less of a stack and more of a matrix, involving solutions that are interoperable and flexible. This modern approach offers several key advantages:
Interoperability and Flexibility: The new factory matrix will ensure seamless integration across various systems and platforms, enabling smoother communication and data exchange. This flexibility allows manufacturers to adapt quickly to changing requirements.
Avoidance of Vendor Dependency and Customization: By minimizing reliance on single vendors, manufacturers can mix and match solutions from different providers, reducing risk and promoting innovation. This approach also gives manufacturers the freedom to customize various solutions to meet their unique needs.
This transition will undoubtedly take time, but as the industry faces challenges such as a shortage of skilled labor, an aging workforce, inflation, and shorter product innovation cycles, adopting these new technologies will be essential for manufacturers to stay competitive.
Industry 4.0 Innovators
While my last post showed a map of players based on function, I’ve since transitioned to categorizing companies based on value proposition. This is due to the often overlapping and intertwined nature of the Production and Operations Management functions which, together, serve as the heart of the factory. The three main categories of value proposition include:
Silo Breakers: Software solutions that aim to bridge the traditionally siloed factory layers.
Example(s): Collecting and aggregating data from various machines on the shop floor into a digestible dashboard for the management layer.
Sample KPI: Higher revenue from better production scheduling and increased capacity utilization.
Method Modernizers: Hardware and software solutions that replace antiquated processes or methods.
Example(s): Industrial robotics, additive manufacturing, digital work instructions.
Sample KPI: Higher production consistency and quality and a lower defect rate.
Uptime Optimizers: Hardware and software solutions to enable machinery perform at its peak and prevent unnecessary downtime.
Example(s): Anomaly detection for preventative maintenance.
Sample KPI: Higher revenue from reduced downtime and lower maintenance costs.
As always, if you think I missed highlighting a company or if you are in the Smart Manufacturing space, please reach out - I love to connect!
About Maverix Private Equity:
Maverix seeks to make significant minority investments in disruptive companies with proven business models who have potential for rapid growth. We seek investments primarily in Canada and the US with a focus on the Consumer Retail, Healthcare & Wellness, Financial Services, Transportation & Logistics, and Work, Live, Play & Learn sectors. Our investment size ranges from US$20mm to $100mm+.